Introduction:
Diesel generators play a critical role in providing backup power during emergencies and supporting various industrial applications. As such, it is essential to ensure that these generators are reliable, efficient, and well-maintained. Validation inspection is a crucial process that helps verify the performance and integrity of diesel generators, ensuring they are ready to provide power when needed. In this article, we will delve into the importance of diesel generator validation inspection, its key components, and best practices to ensure optimal performance and longevity.
Importance of Diesel Generator Validation Inspection:
Diesel generators are commonly used in a wide range of applications, including hospitals, data centers, telecommunications facilities, and construction sites. These generators must be regularly inspected and maintained to ensure they can operate efficiently and reliably during power outages or other emergencies. Validation inspection is a systematic process designed to verify the performance, functionality, and safety of diesel generators, helping to identify potential issues before they escalate into costly failures.
One of the primary reasons why diesel generator validation inspection is crucial is to ensure compliance with regulatory standards and industry best practices. Many regulatory bodies, such as the National Fire Protection Association (NFPA) and the Occupational Safety and Health Administration (OSHA), have established guidelines for the maintenance and testing of emergency power systems, including diesel generators. By conducting validation inspections, organizations can demonstrate their commitment to compliance and safety standards, reducing the risk of penalties and liabilities in the event of an inspection or audit.
Moreover, diesel generator validation inspection helps organizations mitigate the risk of unexpected downtime and disruptions caused by generator failures. Regular inspections can uncover hidden issues, such as fuel system leaks, coolant leaks, or electrical faults, that could compromise the performance of the generator during a power outage. By proactively addressing these issues through validation inspection, organizations can minimize the risk of costly repairs, downtime, and lost productivity, ensuring the uninterrupted operation of critical systems and equipment.
Key Components of Diesel Generator Validation Inspection:
A comprehensive diesel generator validation inspection encompasses several key components that evaluate the various aspects of the generator's performance, functionality, and safety. These components are essential for identifying potential issues, assessing the overall condition of the generator, and determining the necessary maintenance and repairs to optimize its performance. The following are some of the key components of diesel generator validation inspection:
1. Visual Inspection:
Visual inspection is the first step in the validation inspection process and involves a thorough examination of the external components of the diesel generator. During this inspection, technicians look for signs of physical damage, corrosion, leaks, and loose connections that could indicate potential problems. Common areas that are inspected visually include the engine, alternator, fuel system, cooling system, exhaust system, and control panel. Any anomalies or abnormalities identified during the visual inspection are documented and addressed in the subsequent steps of the inspection process.
2. Functional Testing:
Functional testing involves running the diesel generator under load to evaluate its performance under simulated operating conditions. This testing typically includes conducting a load bank test to measure the generator's output voltage, frequency, and load capacity. By subjecting the generator to varying loads, technicians can assess its ability to maintain stable voltage and frequency levels, as well as its response to changes in load demand. Functional testing helps verify that the generator is capable of meeting the power requirements of the connected loads and ensures its reliability during actual power outages.
3. Electrical System Inspection:
The electrical system inspection focuses on evaluating the integrity and performance of the generator's electrical components, including wiring, connections, breakers, relays, and control circuits. Technicians check for loose connections, damaged insulation, overheating, and other electrical faults that could affect the generator's operation. They also verify the proper functioning of protective devices, such as overcurrent protection, ground fault protection, and voltage regulation systems, to ensure the safety and reliability of the electrical system. Any deficiencies or abnormalities identified during the electrical system inspection are addressed promptly to prevent potential hazards and failures.
4. Fuel System Inspection:
The fuel system inspection is critical for ensuring the proper storage, supply, and combustion of fuel in the diesel generator. Technicians inspect the fuel tank, fuel lines, filters, injectors, and pumps for leaks, contamination, blockages, and other issues that could impair the performance of the generator. They also verify the quality and quantity of fuel in the tank, as well as the integrity of the fuel delivery system, to prevent fuel-related problems during operation. Proper maintenance of the fuel system is essential to ensure the efficient and reliable operation of the generator and prevent fuel-related failures.
5. Cooling System Inspection:
The cooling system inspection focuses on evaluating the effectiveness and condition of the generator's cooling system, which is essential for regulating the temperature of the engine and preventing overheating. Technicians inspect the radiator, coolant level, hoses, water pump, thermostat, and fan for leaks, blockages, corrosion, and other issues that could impede the cooling process. They also check the coolant concentration, pH level, and condition to ensure proper cooling performance and prevent engine damage. Regular maintenance of the cooling system is crucial to prevent overheating and ensure the longevity of the generator's engine.
6. 300kw diesel generator :
The exhaust system inspection is aimed at verifying the proper operation and condition of the generator's exhaust system, which is responsible for removing combustion gases and minimizing noise levels. Technicians inspect the exhaust manifold, muffler, exhaust pipes, silencer, and emissions control devices for leaks, corrosion, blockages, and other defects that could affect the exhaust flow and emissions. They also check for excessive exhaust backpressure, exhaust leaks, and carbon buildup, which can reduce the efficiency and performance of the generator. Proper maintenance of the exhaust system is essential to ensure compliance with emissions regulations, prevent exhaust-related issues, and minimize environmental impact.
7. Control System Inspection:
The control system inspection focuses on evaluating the functionality and reliability of the generator's control panel, monitoring devices, sensors, and safety interlocks. Technicians check the operation of the control panel interface, alarms, gauges, meters, and switches to ensure they function correctly and provide accurate information about the generator's status. They also verify the proper operation of safety interlocks, such as low oil pressure shutdown, high coolant temperature shutdown, and overspeed protection, to prevent catastrophic failures and protect the generator from damage. Regular testing and calibration of the control system components are essential to ensure the safe and efficient operation of the generator during emergencies.
Best Practices for Diesel Generator Validation Inspection:
To ensure the effectiveness and reliability of diesel generator validation inspection, organizations should adhere to best practices that promote thoroughness, accuracy, and compliance with industry standards. By following these best practices, organizations can optimize the performance and longevity of their diesel generators, minimize the risk of failures, and ensure a reliable source of backup power when needed. The following are some best practices for conducting diesel generator validation inspection:
1. Develop a Comprehensive Inspection Checklist:
Organizations should develop a detailed inspection checklist that covers all critical components and systems of the diesel generator. The checklist should include specific inspection tasks, testing procedures, acceptance criteria, and documentation requirements for each component, ensuring that no aspect of the generator is overlooked during the inspection. By following a structured checklist, technicians can systematically evaluate the generator's performance, identify potential issues, and record their findings accurately for further analysis and action.
2. Schedule Regular Inspection and Maintenance:
Regular inspection and maintenance are essential for ensuring the optimal performance and reliability of diesel generators. Organizations should establish a preventive maintenance schedule that includes periodic validation inspections, routine servicing, and component replacements based on the manufacturer's recommendations and industry standards. By adhering to a proactive maintenance schedule, organizations can detect problems early, prevent unexpected failures, and extend the operational life of the generator.
3. Engage Qualified Technicians:
Validation inspection of diesel generators requires specialized knowledge, skills, and experience to perform effectively and accurately. Organizations should engage qualified technicians who are trained in diesel generator maintenance, testing, and troubleshooting to conduct the inspection. Technicians should have the necessary certifications, such as those from the Electrical Generating Systems Association (EGSA) or the National Institute for Certification in Engineering Technologies (NICET), to ensure they have the expertise to assess and maintain diesel generators effectively.
4. Utilize Advanced Diagnostic Tools:
Advanced diagnostic tools, such as infrared thermography cameras, vibration analyzers, power quality analyzers, and digital multimeters, can enhance the effectiveness of diesel generator validation inspection by providing valuable insights into the condition and performance of the generator. These tools enable technicians to detect hidden issues, measure critical parameters, and troubleshoot problems more efficiently than traditional inspection methods. By utilizing advanced diagnostic tools, organizations can improve the accuracy and thoroughness of the inspection process, leading to better maintenance outcomes and enhanced generator performance.
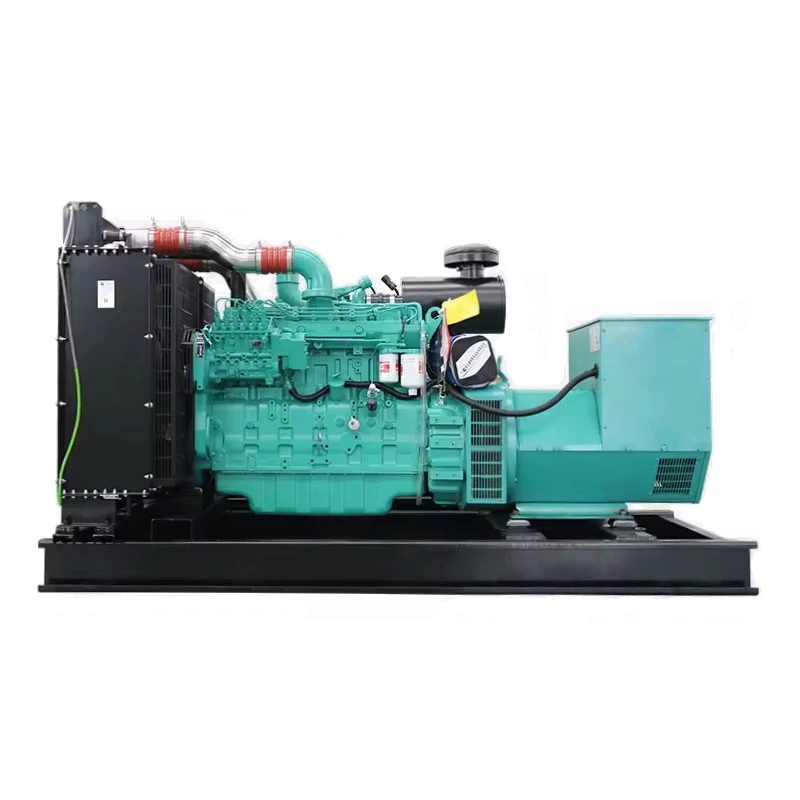
5. Document Inspection Findings and Recommendations:
Accurate documentation of inspection findings, test results, and maintenance recommendations is essential for tracking the condition of the diesel generator, identifying trends, and prioritizing corrective actions. Organizations should maintain comprehensive records of each validation inspection, including inspection reports, test data, maintenance logs, and repair histories, to create a complete maintenance history of the generator. Documentation also enables organizations to demonstrate compliance with regulatory standards, track maintenance costs, and make informed decisions about the repair and replacement of generator components.
6. Implement Corrective Actions Promptly:
Upon completing the validation inspection, organizations should prioritize and implement corrective actions to address any deficiencies or issues identified during the inspection. Timely resolution of problems is crucial for preventing further damage, improving the performance of the generator, and ensuring the safety of personnel and equipment. Organizations should allocate resources, assign responsibilities, and establish timelines for completing the corrective actions, taking into account the severity and urgency of each issue. By addressing problems promptly, organizations can maintain the reliability and efficiency of the diesel generator and minimize the risk of failures.
Conclusion:
Diesel generator validation inspection is a critical process that helps organizations verify the performance, functionality, and safety of their backup power systems. By conducting regular validation inspections, organizations can ensure compliance with regulatory standards, prevent unexpected failures, and maintain the reliability and efficiency of diesel generators. Key components of validation inspection, such as visual inspection, functional testing, electrical system inspection, fuel system inspection, cooling system inspection, exhaust system inspection, and control system inspection, are essential for evaluating the various aspects of the generator's performance and identifying potential issues. Adhering to best practices, such as developing a comprehensive inspection checklist, scheduling regular inspection and maintenance, engaging qualified technicians, utilizing advanced diagnostic tools, documenting inspection findings and recommendations, and implementing corrective actions promptly, can enhance the effectiveness and reliability of diesel generator validation inspection. By following these best practices, organizations can optimize the performance and longevity of their diesel generators, ensuring they are ready to provide backup power when needed.